At a total bridge length of 4.6 km, central span of 2 km and total bridge tower height of 318m, the 1915Çanakkale Bridge in Turkey is the longest mid-span and highest tower suspension bridge in the world.
Named in remembrance of the Çanakkale Battle during World War I, the bridge connects the village of Sütlüce, 10 km south of the town of Gelibolu (Gallipoli) on the European side, with Lapseki on the Asian side. This connectivity reduces the previous 1.5-hour ferry journey across the Çanakkale Strait (Dardenelles) to six minutes and provides a faster and more cost-effective freight transport alternative to the Istanbul Strait passage.
The large-scale construction project which started in 2017 demanded an entirely new heavy lifting approach that could help minimise construction costs and the risks associated with working around the clock over water in an area prone to earthquakes and exposure to high-speed winds. To meet the project deadlines, the cranes would need to be available 24/7 with an average daily utilisation of 20 hours.
After a competitive tender process including some of the world’s leading craneage companies, the consortium of Turkish-Korean joint venture partners DL E&C, Limak, SK ecoplant and Yapi Merkezi (DLSY) that won the construction contract opted for Australian heavy lifting expert Marr Contracting (The Men from Marr’s).

Marr’s craneage methodology helped deliver the project 18-months ahead of schedule, and the bridge opened to the public in March 2022. The success of this methodology could change the way bridges and other large-scale construction projects of this nature are delivered in the future.
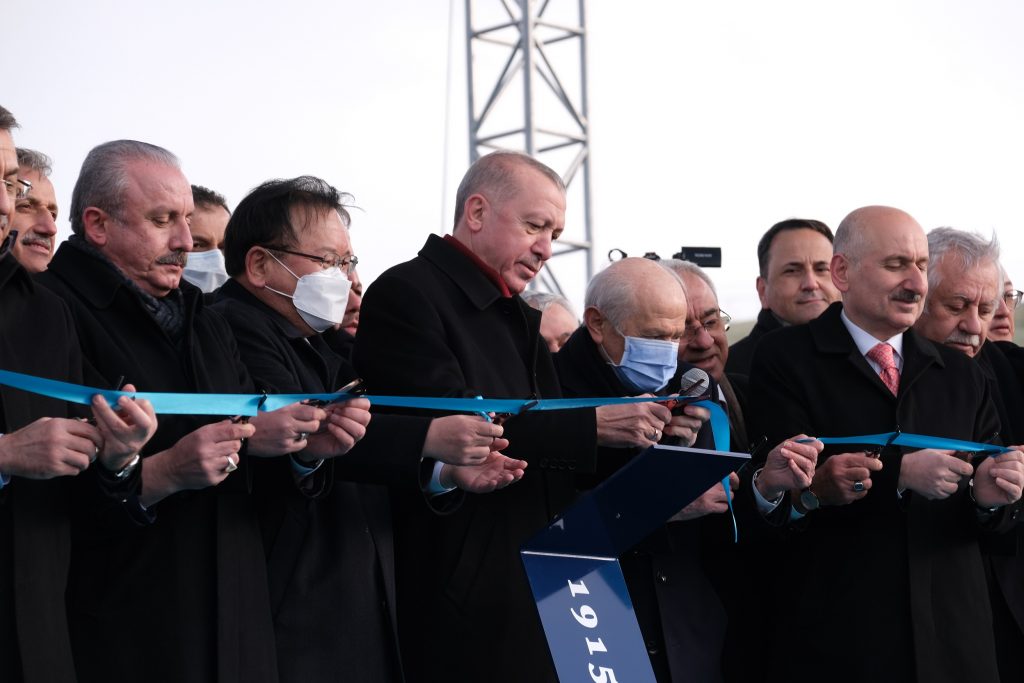
DLSY engaged with Marr Contracting early in the design stage of the project. The initial construction methodology proposed for the 318m bridge towers was the traditional approach to lift panels weighing up to 20 tonnes one at a time and weld them on site, which would require many lighter lifts. Marr Contracting suggested an alternative approach, to modularise the panels in larger sizes, build the modules off-site in pieces weighing up to 160 tonnes, and lift them in single pieces.
The craneage methodology would require only two of Marr’s 300-tonne-capacity M2480D heavy lift luffing jib (HLL) crane, the largest capacity tower crane in the world. By lifting heavier modularised components instead of lifting smaller components one-by-one and then welding on-site, the safety risks of lifting and the total number of lifts could be reduced significantly.
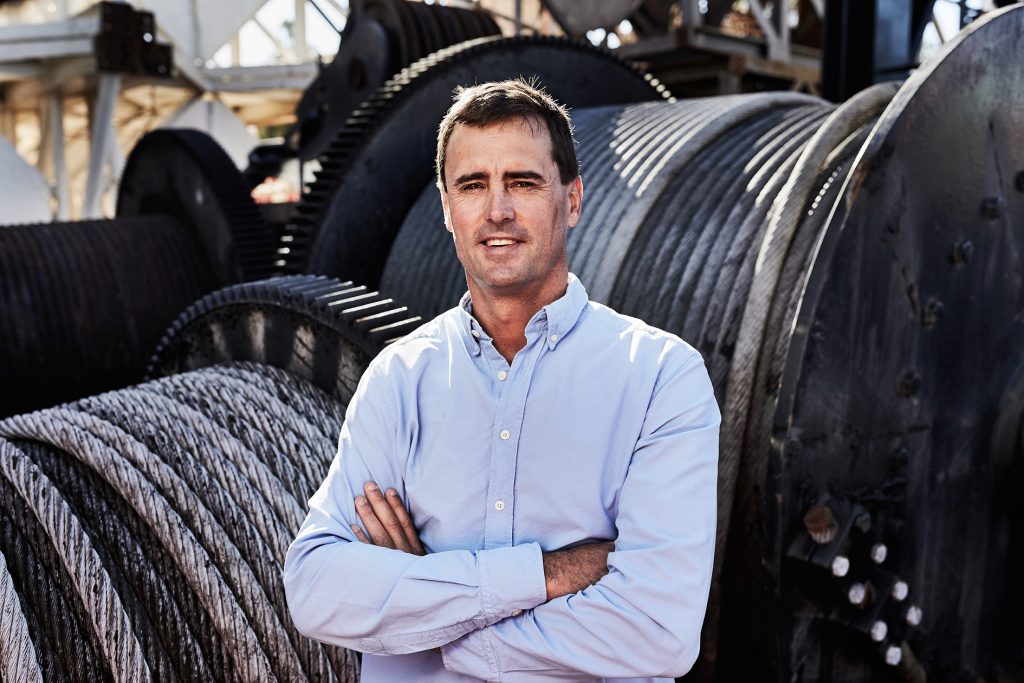
Simon Marr, managing director, Marr Contracting, says: “The DSLY consortium had a clear idea about how they wanted to build the project, but they needed a craneage partner who could think outside the box to bring that vision to life. DSLY aimed to reduce the construction time, associated risks, and project costs and improve safety as much as possible. Getting us involved early in the design stage and our collaboration thereafter was key to the success of this project because that helped align our lifting and construction methodologies.”
Marr’s scope of works on the construction of the high bridge towers included engineering the heavy lift crane solution involving its integration into the temporary and permanent works, and the installation, climbing, operation, maintenance and dismantling of the two M2480D HLL cranes.
Using two of the world’s largest capacity heavy lift luffing tower cranes allowed for prefabricated, modularised panels weighing up to 160 tonnes to be manufactured off site and transported to site to be lifted in one piece. Marr’s solution reduced the number of lifts on the project to approximately one-eighth of the lifts planned.
“The sheer lifting capacity of our M2480D cranes allowed for fewer, heavier crane lifts. This helped to de-risk the project and protect the construction schedule because off-site assembly is faster, safer and more accurate, than welding multiple sections at height,” says Simon.
Marr’s 18-month engagement on the project between 2019 and 2021, saw two world first engineering feats – (1) the placement of the two M2480Ds in a single lift operation 1km offshore in the Canakkale Strait, and (2) the heaviest crane lift at height during the positioning of the upper cross beams on the bridge towers.
During April to August 2019, the two 330-tonne capacity M2480D HLL cranes were shipped from Australia to a dry dock at Gallipoli (Gelibolu), and specialised equipment for the project were manufactured in Marr’s Middle Eastern fabrication facility. The cranes were assembled onshore, on purpose-built quayside foundations.
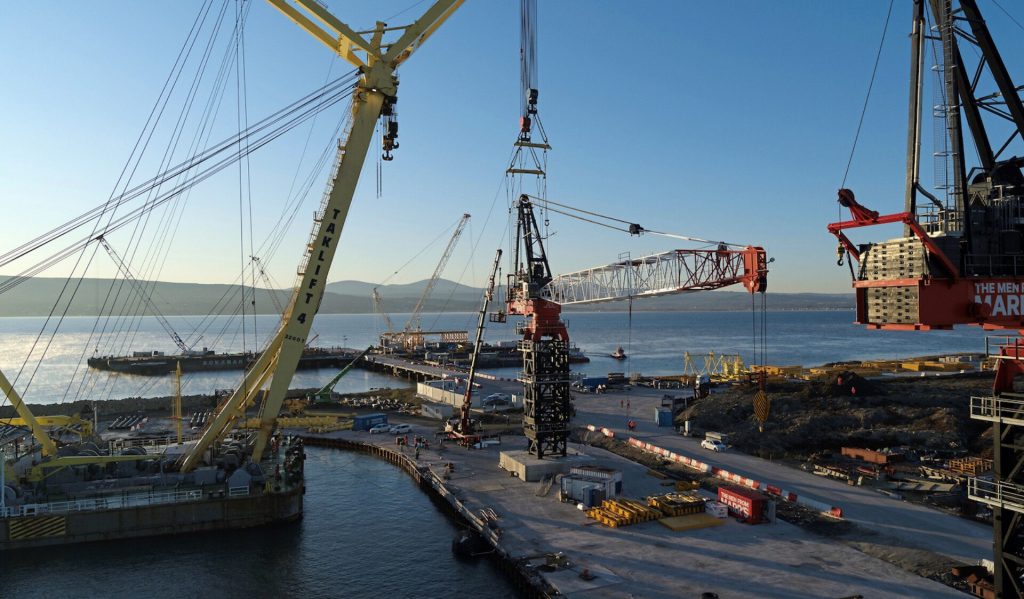
In November 2019, the cranes, each weighing 600 tonnes, were lifted from the quayside as complete units by a 2,200-tonne capacity Taklift 4 floating heavy barge crane and transported a kilometre offshore to the bridge tower caisson in the middle of the Dardanelles (Çanakkale Strait), where they were successfully installed in a one-day operation. This was the first time a crane of this size was lifted fully assembled.
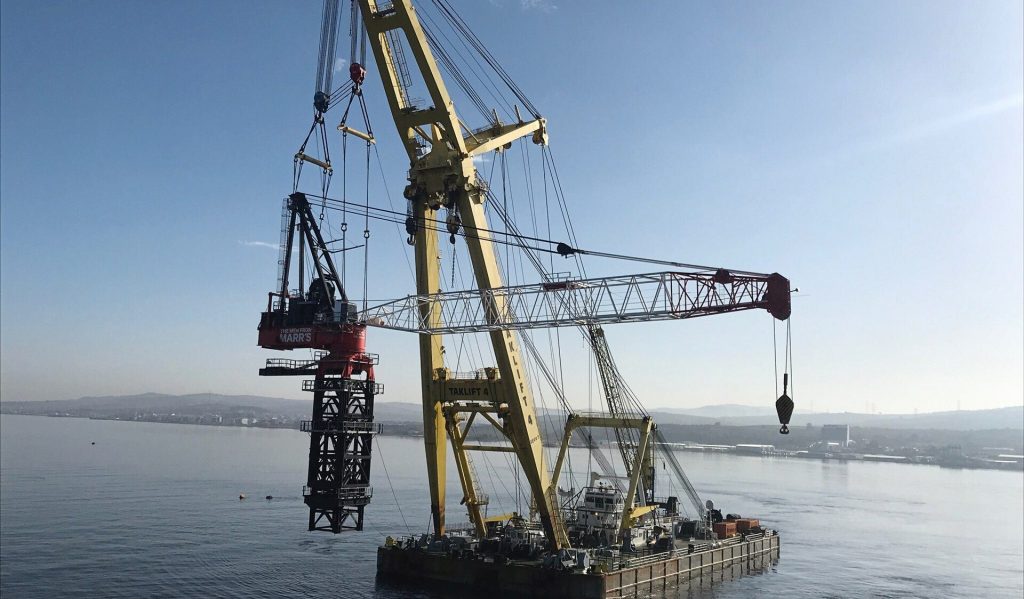
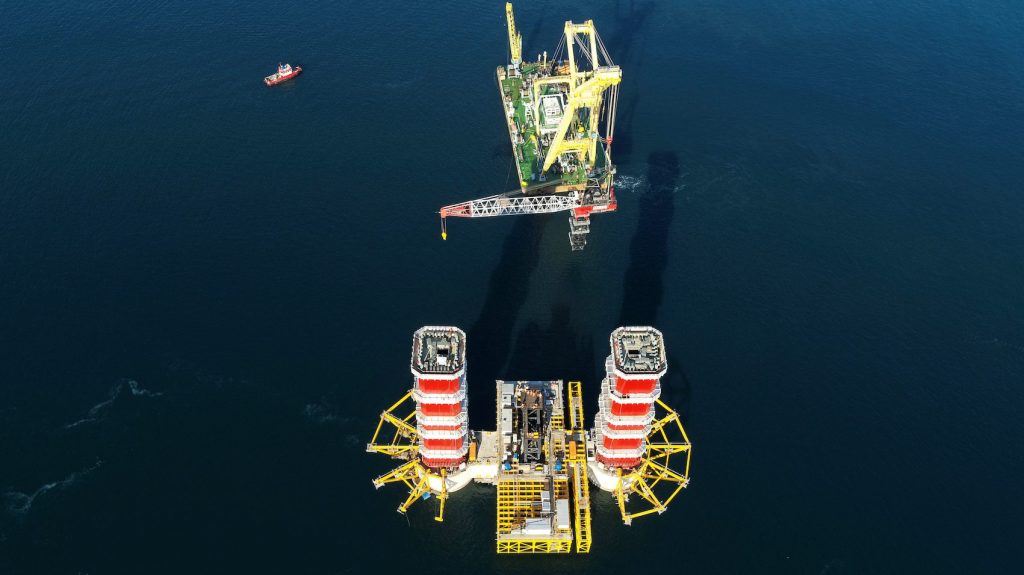
After climbing the cranes to their final height of 328 m, the next major milestone was the installation of the upper cross beam. In June 2020, the M2480D positioned 328 m above the water took approximately 30 minutes to lift a 155-tonne piece of the upper cross beam to its position 318 m above sea level, creating a new world record for the heaviest lift at height.
In June 2020, the installations of the centre sections of the upper cross beam on the Asian and European sides of the Çanakkale Strait were completed within 24 hours, and the final centrepieces were installed on both sides of the bridge at a final height of 318m.
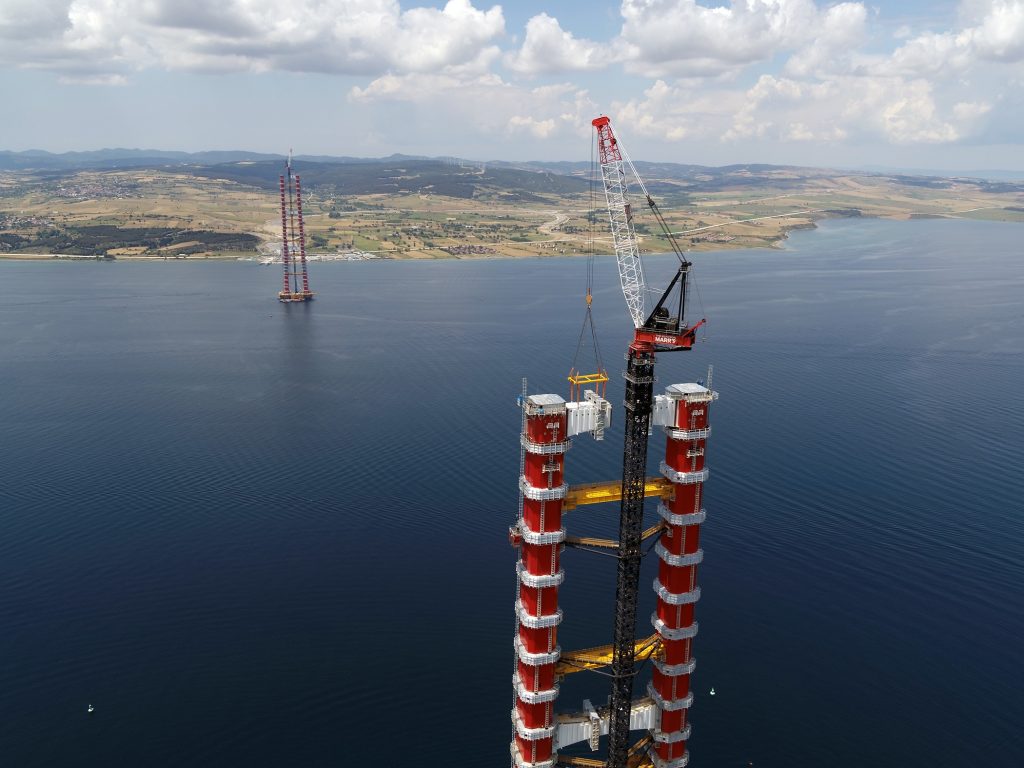
By November 2020, construction of the bridge towers was completed ahead of schedule. Working at 24/7 availability, both M2480Ds worked at an average utilisation rate of 20 hours per day to complete 8 x 160-tonne lifts, 36 x 150-tonne lifts and 208 x 100-tonne lifts. After the construction of the bridge towers, the M2480D HLLs were climbed down the completed bridge towers and safely recovered.
“We are incredibly proud to have been part of this amazing project and the successes achieved for Marr and our client is a case study in how early engagement and true collaboration can drive a successful outcome on any large-scale construction project. The unparalleled lifting capacity of the M2480D HLL was a game changer for this project and could forever change the way our industry looks at building bridges in the future,” says Simon.