Much has been talked about heavy vehicle on-road transportation, including the immediate future of electrified long-haul transport demonstrating significant progress towards series production. Even better is the long-haul trucking industry’s interest in hydrogen-powered fuel and hydrogen combustion due to its faster refuelling, greater range, and lower weight compared to batteries.
However, another transportation sector under pressure to decarbonise is off-road vehicles, equipment, and machinery used in construction, mining, agriculture, and ports. According to the International Council on Clean Transportation (ICCT), in the US, non-road vehicles – mainly agriculture and construction equipment – account for almost three-quarters of the fine particulate matter (PM2.5) and one-quarter of the nitrogen oxides (NOX) emitted from mobile sources. In Europe, non-road vehicles contribute approximately one-quarter of the PM2.5 and more than 15% of the NOx emitted from mobile sources.
Moreover, emissions from construction machinery represent the third largest share of a building’s lifetime greenhouse gas emissions and are reportedly responsible for 50,000 annual deaths due to air pollution, prompting countries worldwide to take more severe action.
This lack of responsibility is mainly because the emission-control strategy for off-road vehicles, including tailpipe emission standards and in-use compliance, lags years behind that of on-road heavy-duty vehicles, due to less targeted legislation in the sector, even though the vehicles share many similarities in the design of diesel engines and exhaust emission control technologies, according to the ICCT.
But, with global initiatives such as net-zero by 2050 and reduction in carbon emissions taking up priority, industry veterans and originals equipment manufacturers (OEMs) are being forced to find ways to lessen diesel’s carbon impact. Moreover, while diesel has powered heavy vehicles and machinery for decades, other alternative forms of power are slowly becoming popular, although many have not yet reached their full potential, nor have they developed the infrastructure for a 100% transition.
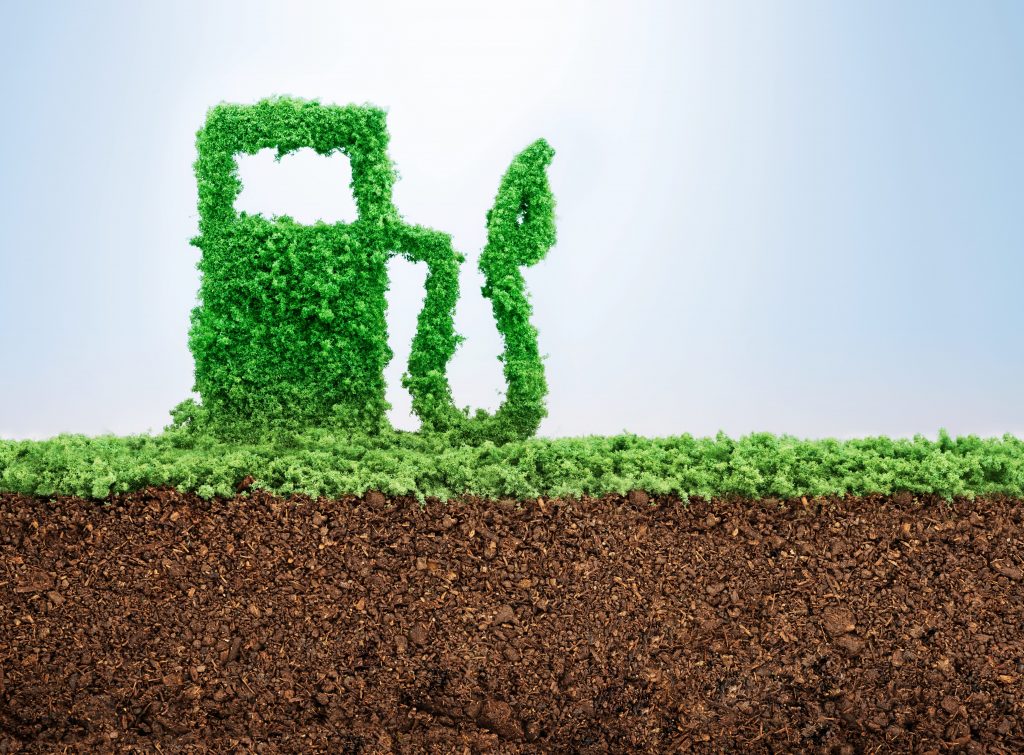
Fuel flexibility for construction machinery
According to the US Department of Energy, more than a dozen alternative fuels are in production or under development for use in alternative fuel vehicles and advanced technology vehicles. Of these, the most popular types of alternative fuels include natural gases, ethanol, propane, hydrogen fuel cells, and electric vehicles.
Use cases of propane and natural gas include power pavers due to its effectiveness at heating asphalt and usage in trucks, respectively, while liquefied petroleum gas-powered rollers, which burn cleaner, are proposed for use in job sites where emissions are critical. Natural gas is also considerably cheaper than diesel and gasoline when measured on a gallon equivalent basis and has saved funds for operators of dumpster trucks and commercial vehicles, which run on compressed natural gas.
Similarly, an alternative fuel used in all diesel-powered Volvo Construction Equipment is hydrotreated vegetable oil (HVO), a biodiesel that uses hydrogen – not methanol – as a catalyst, which results in propane production. An added benefit of HVO is that switching to it is an easier solution than other alternative fuels since it uses the same type of tanks and pumps.
Nonetheless, while biodiesel is considered a cleaner and greener alternative, it is not as fuel-efficient as petroleum diesel, which may hinder its usage among users.
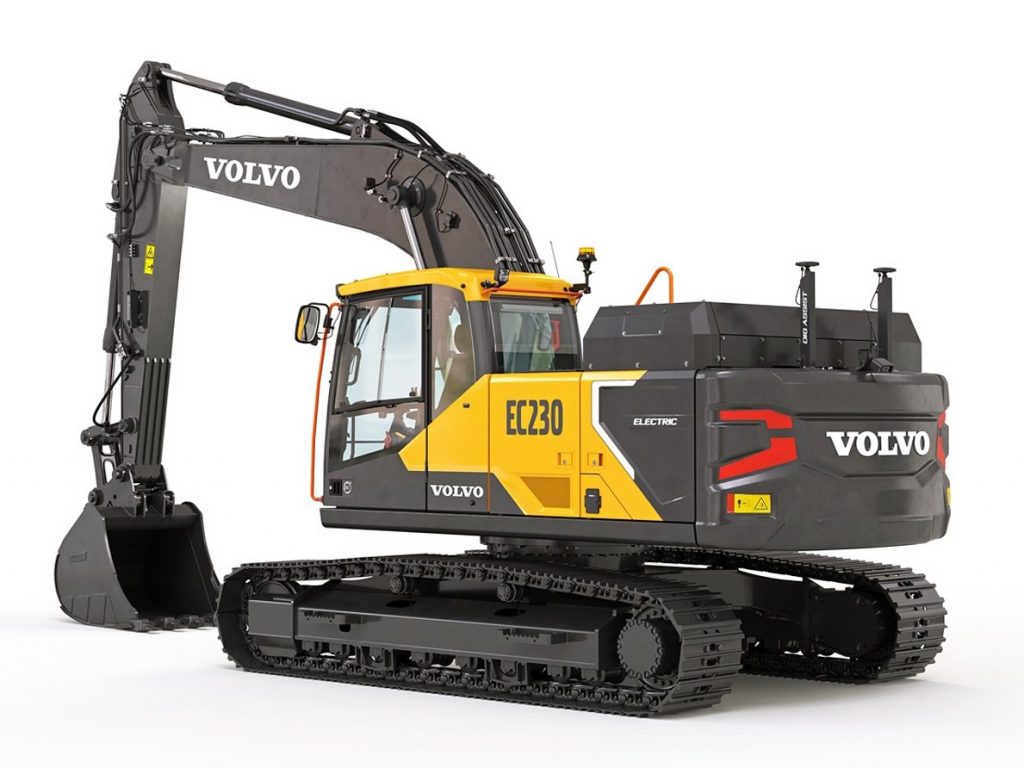
Electric is in no way left behind, and options are certainly growing. Early last year, Volvo, for instance, began selling its electric compact excavators and wheel loaders in North America and expanded its offerings to include five machines. Meanwhile, in a ground-breaking step for the company, it announced the 22 tonne EC230 electric excavator, which is being designed and built at its facilities in South Korea to suit a broader Asian customer base. While this is not yet available in the market, it is the first time the company has electrified a larger excavator as a customer pilot; one which is expected to achieve 60-70% reduction in energy running costs compared to the diesel-powered EC220.
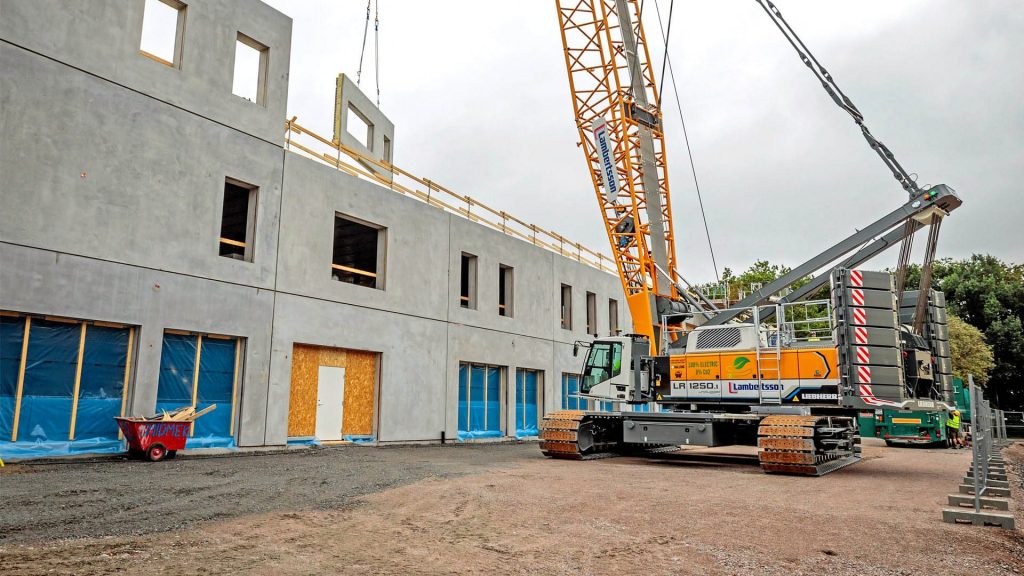
In 2020, Liebherr unveiled the world’s first battery-powered crawler crane – the LR 1250.1 unplugged – which can be connected to an unconventional electric supply or without a cable, which the company claims have made no compromise to its performance or availability.
Hydrogen is another vastly explored alternative to fuels. Currently, construction equipment prototypes use hydrogen as a fuel cell that charges a battery-electric machine or to fuel an internal combustion engine, according to the Association of Equipment Manufacturers. OEMs are making fuel breakthroughs with new machineries, such as JCB’s 20-tonne 220X excavator powered by a hydrogen fuel cell, Volvo’s HX04 – the world’s first articulated hauler prototype; Hyundai’s fuel-cell excavators and forklifts, and SANY’s dump truck and mixer truck, among others.
Hydrogen fuel cell construction vehicles predominantly have five critical advantages, including zero pollution, with only water and heat being discharged, in addition to long battery life, more power, enhanced weather adaptability, and extra safety considerations, according to SANY’s R&D team.
Meanwhile, JCB, the first construction company in the world to unveil a working prototype of an excavator powered by hydrogen, has also developed a hydrogen-fuelled engine, which can be used in various equipment, including loadalls, excavators, and backhoes.

Hyundai’s hydrogen-powered forklifts and medium/large capacity excavators are expected to begin mass production and distribution in 2023. Concerning this, the company stated that hydrogen fuel cells are much easier to expand, making them a much more logical choice for large forklifts or excavators than lithium batteries, which have been marred by structural issues limiting various attempts to increase battery capacity.
It is clear that many OEMs are building prototypes and utilising hydrogen fuel-cell technology, which is getting its deserved traction; however, it should be seen as a complementary technology with electric power to truly achieve zero-emission end-products. Furthermore, while hydrogen makes more sense for larger machinerywith extensive energy demands and more utilisation, electric makes more sense for compact, light-duty vehicles due to battery charge times and infrastructure limitations.
Breaking the roadblocks
However, industry experts note some significant challenges in electric machines, including the downsides associated with run-time-per-charge and recharging time.
At the same time, while electric charging infrastructure is becoming more widely available in urban areas for customer use, construction job sites that aren’t even on the grid experience more access difficulties – one of the reasons many OEMs are selling chargers with their machines.
Solar charging is another potential point of examination.
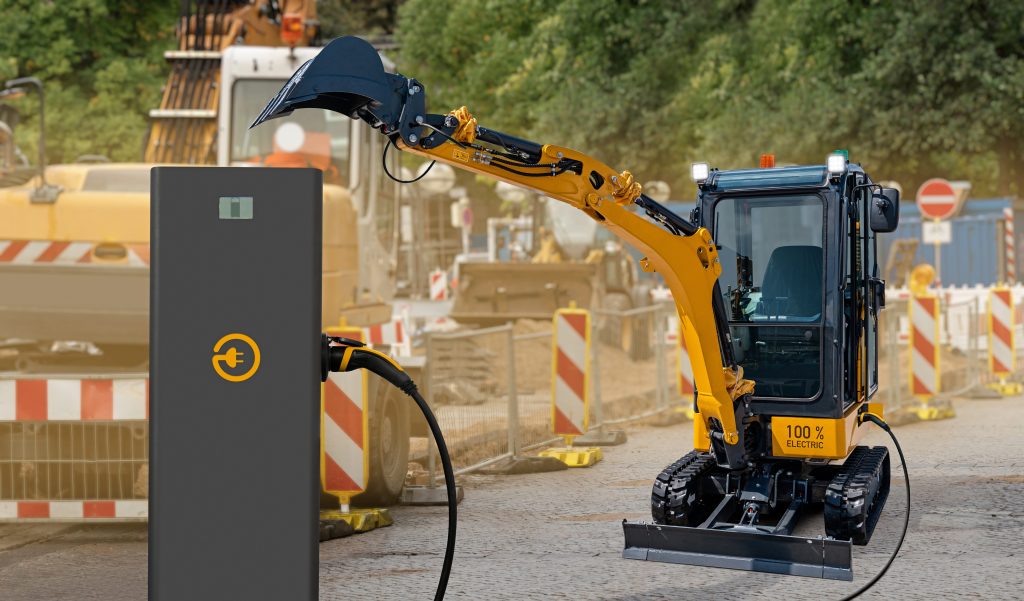
In an exclusive conversation with us, Frank Bernthaler, the COO of Admiral Mobility, which recently launched the largest single electric commercial truck order in the GCC, said it is only a question of time before the trends in commercial electric vehicles will be reflected in other heavy vehicle industries. While the developments in on-road and off-road vehicles are far apart, the challenges are similar. He noted that hydrogen-based solutions will become a part of long-haul transport in the future, and highlighted the need to provide an extensive charging network to manage routes for electric-powered vehicles.
Long-term vision
Meanwhile, experts record no technical barrier to the mass production of hydrogen-powered machinery, barring prices, supply infrastructure, and government policies. They also noted the importance of private investment and government funding – for instance, Germany will spend approximately $9 billion on hydrogen, while China and South Korea are developing fuel cell and hydrogen production targets.
While the World Economic Forum acknowledges that hydrogen isn’t a direct substitute for coal, oil and natural gas, it sees how hydrogen could account for up to 12% of global energy use by 2050. Additionally, Europe is leading in facilitating a hydrogen-based economy, especially with manufacturers levelling the playing field. An example of this is the Volvo Group and Daimler Truck’s 50:50 joint venture called cellcentric, which has been developing, producing, and commercialising fuel cells in heavy-duty trucks and other areas.
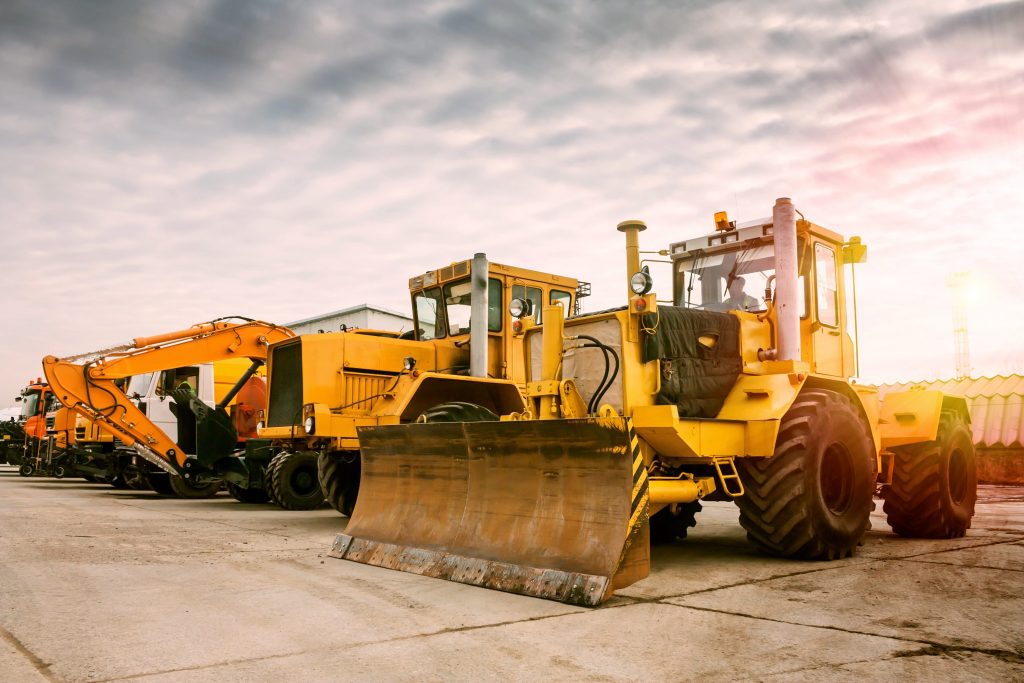
Electric-powered vehicles also reportedly see decreased operating costs, as well as reduced fuel costs, repair frequency, and downtime, according to Caterpillar, which recently unveiled four electric machine prototypes at Bauma 2022. Furthermore, as legislations worldwide become more stringent, heavy industries are expected to become one of the world’s fastest adopters of electric-powered drivetrains, resulting in optimal products and energy recyclability.
Looking ahead, the EV transition appears to be getting closer, so does hydrogen’s future, but a lack of infrastructure is one of the reasons it is being held back in terms of generation and storage. McKinsey’s report stated that over the coming years, there will be a significant increase in the number of hydrogen-powered vehicles on the road, and while passenger cars will contribute to hydrogen consumption and have previously been the focus segment, in the future, around 95% of demand by volume will come from commercial vehicles. It anticipates that by 2030, as many as 850,000 hydrogen-fuelled medium and heavy-duty trucks will be on the road in Europe.
Meanwhile, industry experts note that over the next five to 10 years, hydrogen fuel cell technology, which can be abundantly used in heavy machinery, will become not only environmentally viable but also operationally and economically suitable.