Demolition is difficult, dirty, dangerous work. It is also necessary work. How best to keep workers safe in a demolition environment? Remove them from that environment.
When the persons come out, the robots move in. Robotic demolition has been soaring in popularity. Demolition includes razing structures, but a growing demand for demo comes from retrofitting and repurposing existing structures. That can be done by an operator on a skid steer with an attachment, but dust, fumes, falling debris, and other hazards have driven contractors to seek out other options to keep their workers safe; enter robotic options. There are also demolition settings where the fumes and oxygen consumption of diesel- and even propane-powered equipment are not allowed due to worker safety. Electric robots answer all these concerns.
Compact demolition machines with big-machine performance
The use of electric robotics for demolition machines is nothing new Brokk, which has a product line around remote demolition equipment. Lightweight and compact size are key for many of the jobs where Brokk robots are used, including interior demolition. Many models are within floor and elevator load limits, making transport and setup much easier. All models have lift points and can be craned into position, if necessary. Since demolition robots are purpose-built for the task, their size and weight may not good indicators of their capability.
Jeff Keeling, vice president of sales and marketing at Brokk, states: “It would typically take an excavator three times heavier than a Brokk equipment piece to deliver comparable breaker performance and our four smallest models fit through a standard doorway. We aren’t adding an attachment to an existing piece of equipment. We are designing purpose-built demolition machines for use in confined spaces.”
As is the case with Brook machines, demolition robotic machines are remote-controlled by radio and cable with a range of up to 1,000 feet.
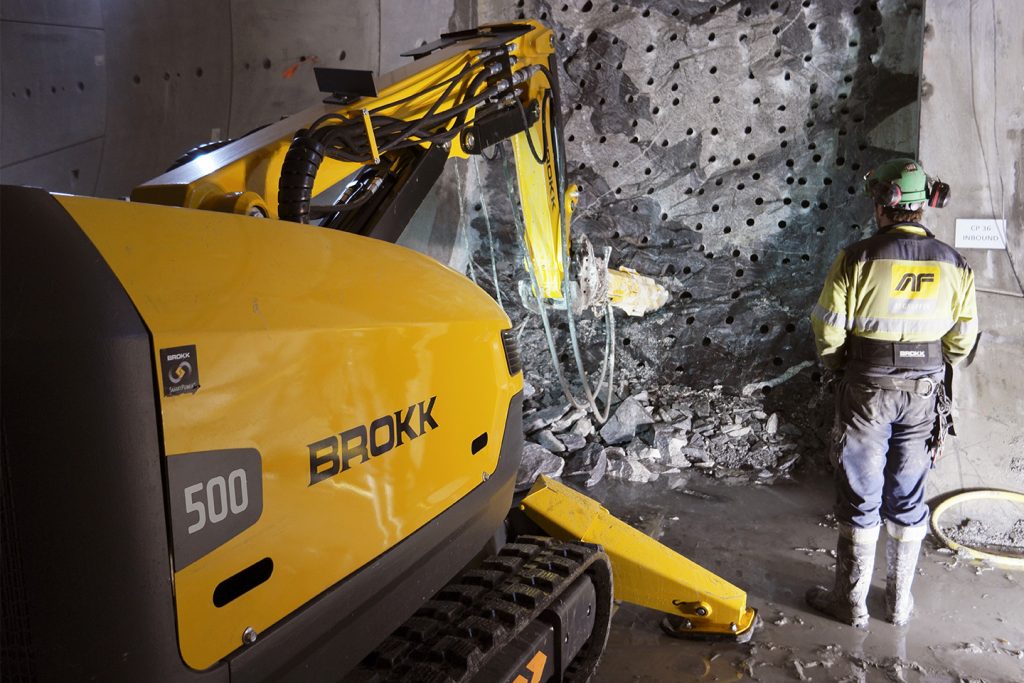
The appeal of electric demolition equipment
Just as electrification is making waves in consumer vehicles and land-moving construction equipment, it continues to affect the future of demolition equipment. While Brokk offers diesel models where their use is appropriate, but their innovations specialize in electric. Power is supplied by plant or building power or by generator if sufficient plant power is not available. Brokk’s electric models require 480-volt service of 20 to 100 amps, depending on the model. Wire gauge also varies by model and length of run.
This raises a question: why not batteries?
“Attachments are huge power consumers,” says Keeling, “and today’s battery technology limits run time to two or three hours, which is clearly not sufficient.”
How is it other electric equipment has longer run times?
Other machines have a lower draw, are hybrids, or have much larger battery packs. Brokk machines, with their emphasis on high power output from compact equipment designed for use in confined spaces, don’t lend themselves to hybrid power or massive, stacked batteries.
In terms of the future of electrification for remote demolition equipment, Keeling states: “We’re always monitoring battery development and it’s conceivable at some point we’ll be able to offer battery-powered models, but battery technology is not at that point yet.”
A full range of demolition attachments
If a company is thinking about investing in a piece of remote-controlled demolition equipment, machine and attachment versatility will be top of mind. Hammers and breakers are the core of Brokk attachments, but they offer a full catalog of tools and attachments specifically designed to provide peak performance from Brokk machines. Examples include digging buckets, concrete crushers, grapples for soft demolition and material handling, steel shears, concrete scabblers, drilling attachments, and splitters. Brokk also has the capability to design and build custom attachments such as plasma cutters and torch tools.
The versatility of attachments has led to versatility in applications. Besides demolition, Brokk is also active in the nuclear power industry, safety, and rescue. As a pioneer in the remote demolition industry, Brokk equipment has a wide tilt range for attachments and also boasts a three-part arm design. These features improve performance in tight spaces but also provide unique angles of attack on faces, floors, and even overhead.
Market conditions for demolition
The switch to robotics has been a hot topic in the manufacturing industry for decades.
“In the early days we’d hear, ‘You’re trying to take away our jobs,’” says Keeling. “Now we hear, ‘Please, help reduce our need for labor.’”
With an ongoing labor shortage, especially a shortage of operators, customers want to cut their need for hourly workers and shuttle their remaining staff to tasks that provide more return to both the company and the employee.
Keeling says downtown renovations are big, with many buildings being repurposed to housing. There’s been a huge shift in the workforce recently, with many employees leaving traditional employment to pursue something else. Many that remain are working remotely, either by their choice or that of their employers. Estimates are that up to 30 percent of workers will be remote by 2025.
Does this open up commercial properties for repurposing? Not yet,” says Keeling, “Commercial property owners are taking a wait-and-see approach before reconfiguring their properties.”
Mention demolition to members of the general public and they recall media footage. Precisely timed detonation of charges. An office tower or casino or bridge turned from form and structure to rubble and dust in just seconds. But demolition work is rapidly morphing into something with more control, more finesse, but no less danger. Electric, robotic demolition machines answer the twin requirements of production and safety as this market continues to evolve.