A number of employee monitoring systems have been introduced in the construction and transportation industries with the aim of making employees safer. Dash cams are being installed into truck cabs, not to record traffic but to record the activities of the driver. Truck companies want to make sure drivers are checking their mirrors, and especially aren’t using their phones when behind the wheel.
The Spot-R fall alert and emergency evacuation system from Triax Technologies monitors employees’ movements to alert safety personnel if the device changes elevation quickly, indicating a fall. It also alerts workers of an emergency evacuation.
RFID tags from Scan-Link Technologies monitor employees’ locations and alerts equipment operators of employees who are located behind the machine.
Some smart watches detect vibration; that technology is used to monitor the ramifications to the body from using power equipment for a long time. Alerts tell the end-user when power tool use exceeds what the body can safety perform, and this is to prevent hand-arm vibration syndrome (HAVS).
Smart helmets monitor several health elements, such as fatigue, heart rate and stress, so workers and management can modify worker’s activities in ways that promote employee health and job site safety and productivity.
Turning historical data into predictive analytics
A lot of times, employee monitoring can lead to policy changes and coaching opportunities.
Jonathan Fava, president, Scan-Link Technologies, explains: “One customer who uses our Scan-Link RFID technology reported to me the following story. We were looking at the number of times equipment operators were alerted to the presence of a nearby worker, and we noticed one person was causing a lot of alerts, so we pulled that individual aside and asked him why. He explained that he’s the flagger and that when operators load the machine onto a float, he gets up on the float to aid the operator place the machine. We advised him that behavior is unsafe and that he could get struck by the machine or fall of the float. So, we told him a safer way to perform his job and wrote down new safety protocols into our guidelines and training.”
Using historical data to learn how things happen is the first step to promoting safety on the job site. “It’s not enough just to learn how accidents have happened,” says Fava. “The next step is to analyze data in order to prevent accidents from happening.
With all of the employee detections picked up by the Scan-Link system, managers can identify ‘hot spots’—spots where machines detect people the most frequently.
“Using this data, customers can identify areas where a struck-by incident is most likely to occur. Then, customers can make decisions that will decrease the risk of an accident from happening by moving the location of materials, so workers don’t have to walk in a machine’s workspace or by putting up signage warning employees of high-risk areas,” says Fava.
Assisted reality connects two physical worlds
Wearables are also instrumental in merging realities, which is bringing connectivity, productivity and accuracy to job sites.
Exoskeleton and assisted reality headset manufacturer Real Wear just released the second version of their assisted reality headset, called the RealWear Navigator 500. It is sleeker, lighter and is more ergonomic than the previous model (the HMT100) for all-day comfort yet is rugged and durable for use on construction sites and in industrial settings.
The RealWear Navigator 500 features a modular design, a 48-megapixel camera sensor with enhanced zoom capability, low light performance, and is compatible with more than 200 optimized apps. A hot-swappable battery allows for continuous use the whole day.
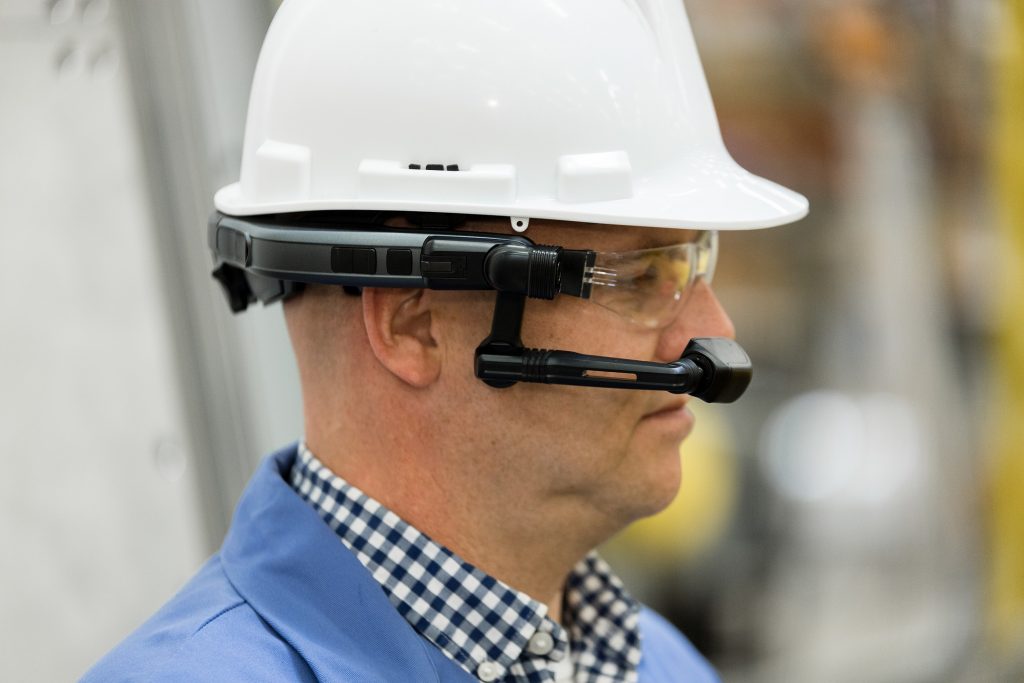
Andrew Chrostowski, chairman and CEO, RealWear Technologies, says: “With the Navigator 500, we wanted to provide scale enterprise solutions as part of the digital transformation movement. Today, we see the acceleration of digital transformation on the future of work, especially since the pandemic. Our device is hands free and keeps you present. You don’t want your head stuck in the metaverse when you’re working around heavy equipment.”
The assisted reality device allows the user to take photo and video at six different zoom levels, as well as make calls. It also accepts audio commands such as “take a picture” or “zoom” or “call Herald” to execute the actions. The device simplifies remote inspections and diagnostics. Workers equipped with the Navigator 500 at job sites can act as the eyes for inspectors and technicians, which enables them to conduct inspections and troubleshooting of equipment remotely, thus saving time and travel costs.
Augmented reality expands by becoming handheld
The Trimble XR10 with Microsoft HoloLens brings a different kind of connectivity and reality. The technology connects virtual reality to physical reality to provide mixed reality.
HoloLens users can see both the physical world and the virtual world; the digital image is overlaid onto the physical world.
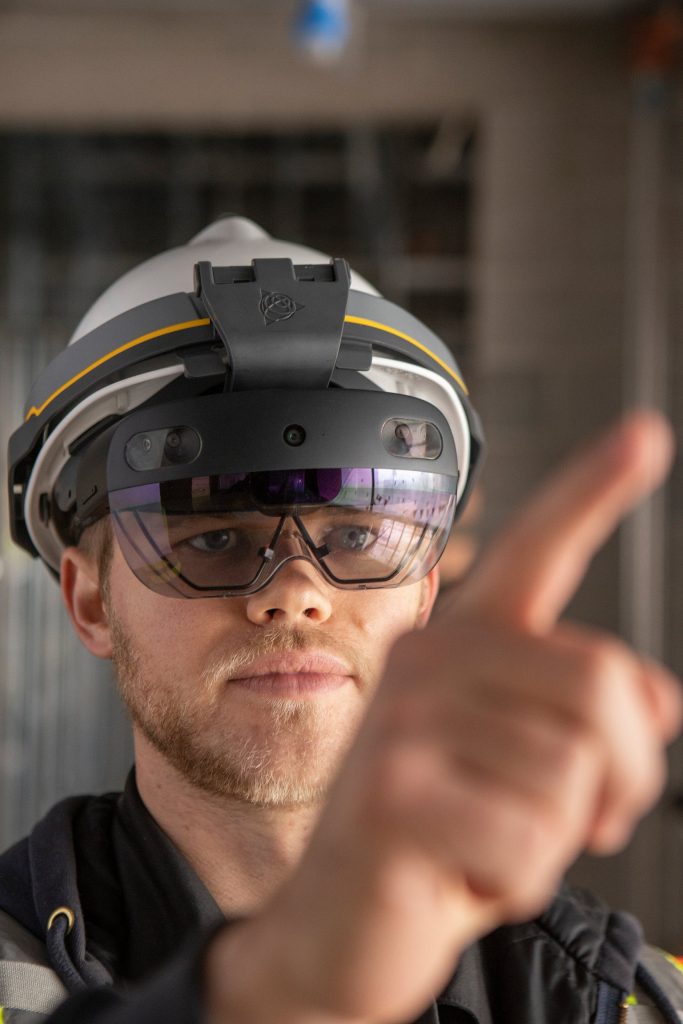
Users no longer need to look at paper designs for what they are installing and then try to map out where that is in the physical world by establishing a frame of reference and taking out the measuring tape; they can simply see, for example, the virtual pipes and their detailed measurements, and install the pipes with high accuracy. They can also see what is being installed nearby, so they can identify potential complications.
Trimble recently expanded the potential for business information modeling (BIM) users to deploy augmented reality on the job site by introducing the Trimble Connect AR app, which is compatible with Trimble Connect. The app is downloaded to a phone or tablet and allows users an augmented reality experience by pushing BIM data to their phone and overlaying it onto images of the real world on the device’s screen.
“This eliminates what can be a costly financial barrier to some customers,” says Martin Holmgren, general manager of building field solutions at Trimble. “And users can interact with Trimble Connect AR users in the digital space. For example, I can leave a message in the digital space with my Trimble XR10 and someone with the Trimble Connect AR app on their phone can detect the message, even weeks later as they walk by the location where it was left and read it. This greatly enhances communications and streamlines workflows.”
Trimble expects people who don’t need to be fully hands-free, such as supervisors, managers, inspectors, and building owners will use it to perform tasks, such as QA/QC, updating punch lists, and measuring construction progress.
“The app allows for the incorporation of AR into workflows that don’t require the user to be hands-free, and we think our app will ultimately drive AR in a much wider range of adoption,” says Holmgren.